Engine oil analysis can provide several cost justifications for trucking companies and fleet managers. Here are some of the key reasons why investing in oil analysis can be financially beneficial.
Extended Oil Change Intervals: Oil analysis can help determine the condition of the engine oil accurately. By identifying the oil’s remaining useful life, trucking companies can extend oil change intervals without risking engine damage. This reduces the frequency of oil changes, saving on the cost of oil, filters, and labour.
The average cost associated with engine oil changes for trucks can vary widely depending on several factors, including the type of truck, the engine, the type of oil used, and the location where the service is performed. Here are some approximate cost ranges to consider:
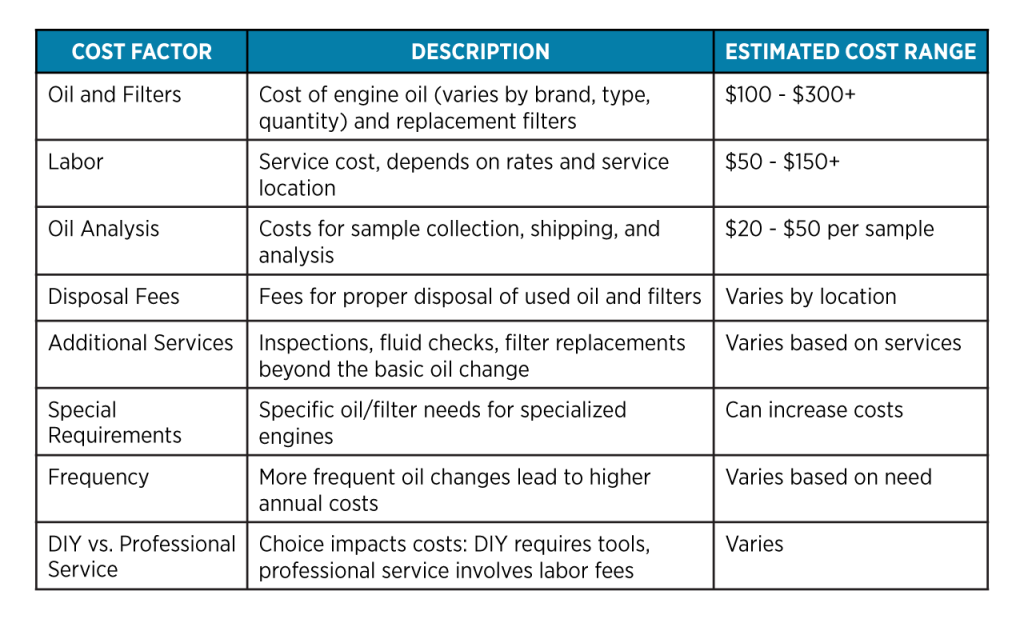
It’s essential to check with your truck manufacturer’s recommendations and consult with your maintenance team or service provider to get a more accurate estimate of oil change costs for your specific trucks and operations. Regular maintenance and oil analysis can help optimize oil change intervals and reduce costs in the long run by extending the life of the engine and reducing the risk of costly repairs.
Preventative Maintenance: Oil analysis can detect early signs of engine wear and potential issues such as coolant leaks, fuel dilution, and contamination. Addressing these problems promptly can prevent more extensive and costly engine repairs or replacements down the road.
The typical repair costs associated with diesel engines can vary widely depending on the make and model of the engine, the type of repair needed, labor rates in the area, and whether the repair is performed by an authorized dealer, an independent mechanic, or in-house maintenance staff. However, here are some common diesel engine repair costs you might encounter:
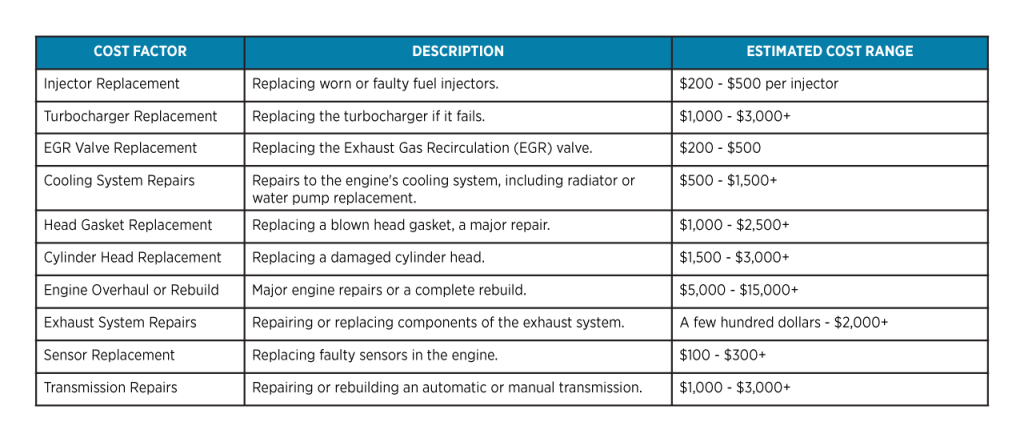
It’s important to note that these are approximate cost ranges, and actual repair costs can vary widely based on factors such as the make and model of the engine, the location of the repair, and whether you are using new or remanufactured parts. Regular maintenance and proactive measures, such as oil analysis and addressing issues early, can help prevent some of these costly repairs and extend the life of the diesel engine. Additionally, warranty coverage may apply to some repairs, depending on the engine’s age and service history.
Reduced Downtime: By identifying potential problems early, oil analysis can help prevent unexpected breakdowns and downtime. This leads to fewer repair-related expenses and ensures that trucks remain in operation, generating revenue.
Downtime costs for over-the-road truck fleets due to engine-related issues can be substantial and can encompass various expenses. The exact costs will depend on several factors, including the severity of the issue, the time required for repairs, the availability of replacement parts, and the location of the breakdown. Here are some typical downtime costs associated with engine-related problems for truck fleets:
- Lost Revenue: One of the most significant costs of engine-related downtime is the loss of revenue. When a truck is out of service, it cannot generate income by transporting goods. The longer the downtime, the more revenue is lost.
- Driver Wages: Even when a truck is not in operation, drivers often need to be paid their regular wages or salary, especially if they are waiting for repairs to be completed. This is a fixed cost that adds up during downtime.
- Towing and Recovery: If a truck breaks down on the road and requires towing to a repair facility, there will be expenses associated with towing services. Additionally, the longer the truck is stranded, the higher the recovery and towing costs may become.
- Rental or Substitute Vehicles: In some cases, fleets may need to rent or lease substitute vehicles to replace the ones undergoing repairs. Rental costs can add up quickly, particularly for long-term downtime.
- Emergency Repairs: Sometimes, trucking companies may opt for emergency roadside repairs to get a truck back on the road temporarily. While this can reduce downtime, it may result in higher repair costs. Parts and Labor Costs: The actual cost of parts and labor to repair the engine issue is a significant factor. This includes the cost of replacement parts, the mechanic’s labor, and any additional services required.
- Storage and Parking Fees: If a truck is stuck at a repair facility or storage yard while waiting for repairs, there may be storage fees or parking fees that accrue.
- Administrative Costs: Managing the logistics of a breakdown, including coordinating repairs, communicating with drivers, and handling paperwork, can result in administrative expenses.
- Late or Missed Deliveries:Engine-related downtime can lead to late or missed deliveries, potentially resulting in penalties, fines, or reputational damage with customers.
- Additional Maintenance: In some cases, engine-related issues may necessitate additional maintenance on related components, further increasing costs.
- Fuel and Idle Time: Idle time while waiting for repairs can lead to fuel consumption and additional operational costs.
- Safety and Compliance: Extended downtime may impact a fleet’s compliance with safety regulations, potentially resulting in fines or penalties.
Minimizing downtime costs is a priority for trucking companies. To mitigate these costs, proactive maintenance practices, such as regular engine oil analysis and comprehensive vehicle inspections, can help identify and address potential issues before they lead to major breakdowns. Additionally, having a well-defined maintenance plan and access to a reliable network of repair facilities can reduce downtime and its associated costs.
Improved Fuel Efficiency: Regular oil analysis can reveal issues that may be negatively impacting fuel efficiency, such as worn piston rings or dirty fuel injectors. Addressing these problems can lead to improved MPG (miles per gallon) and fuel cost savings.
Investing in improved engine performance for over-the-road truck fleets can lead to various costs, but these expenses are often justified by the potential benefits. Here are some typical costs associated with efforts to enhance engine performance for truck fleets:
- Performance Tuning or Upgrades: To improve engine performance, trucking companies may invest in performance tuning or upgrades. This can involve reprogramming the engine’s electronic control module (ECM) or installing aftermarket performance parts. Costs for tuning and upgrades can vary widely but typically range from $500 to $5,000 or more per truck, depending on the extent of modifications.
- High-Performance Parts: Upgrading to high-performance components, such as turbochargers, air intake systems, exhaust systems, or fuel injectors, can lead to additional expenses. These parts can range from a few hundred dollars to several thousand dollars per component.
- Fuel Additives and Treatments: Using fuel additives and treatments to improve engine efficiency and reduce fuel consumption is a common practice. Costs for these products can vary based on the type and brand but are typically a few dollars per treatment.
- Dyno Testing: To optimize engine performance, some fleets invest in dynamometer (dyno) testing services. Dyno testing helps fine-tune engine settings and ensure the engine is operating at peak efficiency. The cost of dyno testing can range from $100 to $500 or more per session.
- Labor Costs: Labor costs are associated with installing performance upgrades, conducting maintenance, and performing engine tuning. These costs depend on the complexity of the work and labor rates in the area.
- Diagnostic Tools and Equipment: Fleets may need to invest in diagnostic tools and equipment to monitor and analyze engine performance data. The cost of these tools varies widely but can range from hundreds to thousands of dollars.
- Training and Certification: Providing training and certification for mechanics and drivers to understand and maintain enhanced engine performance can be an ongoing cost. Training expenses can vary based on the program and the number of participants.
- Regular Maintenance: Maintaining and optimizing engine performance often requires more frequent maintenance, such as oil changes, filter replacements, and inspections. While these are ongoing expenses, they contribute to improved performance.
- Fuel Efficiency Monitoring: Implementing fuel efficiency monitoring systems and software may come with initial setup costs and ongoing subscription fees, depending on the chosen technology.
- Warranty Considerations:Upgrading or modifying engine components can impact warranties. Some manufacturers may void warranties if non-OEM (Original Equipment Manufacturer) parts or unauthorized modifications are used.
- Testing and Validation: Before implementing performance enhancements across a fleet, some testing and validation may be necessary to ensure the modifications meet efficiency and emissions standards.
It’s important to note that while there are upfront costs associated with improving engine performance, these investments can lead to long-term benefits such as reduced fuel consumption, increased horsepower, extended engine life, and improved overall efficiency. Fleet managers should carefully assess the potential return on investment (ROI) to determine whether the costs are justified by the expected improvements in performance and operational savings.
Warranty Compliance: Many truck engine manufacturers require regular oil analysis as part of their warranty agreements. Compliance with these requirements ensures that any eligible warranty claims are honored, saving money on costly engine repairs that would otherwise be the responsibility of the trucking company.
Not applying a warranty program for engine performance in over-the-road truck fleets can lead to various costs and risks. While the specific costs can vary depending on factors such as the age and condition of the fleet and the type of engines used, here are some typical costs and consequences associated with not having a warranty program for engine performance:
- Repair Costs: Without a warranty program, the trucking company is responsible for covering the full cost of engine repairs, including both parts and labor. Major engine repairs can be extremely expensive and can range from several thousand dollars to tens of thousands of dollars per repair.
- Downtime Costs: Extended downtime due to engine issues can result in lost revenue, as the truck cannot transport goods while it is out of service. Downtime costs can add up quickly and vary based on the duration of the repair.
- Towing and Recovery Costs: In the event of a breakdown, the trucking company will need to cover the expenses associated with towing and recovering the vehicle, which can range from hundreds to thousands of dollars.
- Replacement Vehicle Costs: When a truck is undergoing major engine repairs, the fleet may need to rent or lease substitute vehicles to maintain their transportation operations. Rental costs can accumulate during extended repair periods.
- Administrative Costs: Handling repair-related paperwork, coordinating repairs, and managing communication with drivers and repair facilities can result in administrative expenses.
- Late or Missed Deliveries: Engine-related breakdowns can lead to late or missed deliveries, which can result in financial penalties, fines, and damage to the fleet’s reputation with customers.
- Increased Maintenance Costs: Without a warranty program, the trucking company may need to invest more in proactive maintenance to prevent costly engine issues. This includes regular inspections, oil changes, and component replacements.
- Safety and Compliance Risks: Extended downtime can impact a fleet’s compliance with safety regulations, potentially leading to fines or penalties.
- Resale Value: Trucks with documented maintenance records and active warranties often have higher resale values. Not having a warranty program may reduce the resale value of the fleet’s vehicles.
- Risk of Unexpected Expenses: Engine-related issues can arise unexpectedly and can strain the fleet’s finances, as they may not have budgeted for major repairs.
- Inefficient Fuel Consumption: Engine performance issues can lead to reduced fuel efficiency, resulting in higher fuel costs over time.
- Limited Fleet Flexibility: Without a warranty program, the fleet may be less flexible in terms of managing engine-related risks and costs, potentially affecting the company’s overall operational strategy.
- Depreciation: Engines that are not well-maintained and lack warranties may experience accelerated depreciation, leading to a lower overall asset value.
It’s important to note that warranty programs for engine performance can provide financial protection and predictability by covering some or all of the repair costs during the warranty period. When evaluating the costs and benefits, fleet managers should consider the age and condition of their trucks, the expected repair frequency, and the potential savings and peace of mind that a warranty program can offer.
Equipment Longevity: Proper maintenance based on oil analysis results can help extend the life of truck engines and other critical components. This reduces the need for premature equipment replacement, which can be a substantial cost for trucking companies.
Improving engine longevity in over-the-road truck fleets can lead to various costs, but these investments are often justified by the potential benefits, including reduced maintenance costs and extended engine life. Here are some typical costs associated with efforts to enhance engine longevity for truck fleets:
- Regular Maintenance: To improve engine longevity, fleets typically invest in regular maintenance practices, including oil changes, filter replacements, and inspections. While these are recurring expenses, they contribute significantly to engine health and longevity.
- High-Quality Engine Oil: Using high-quality engine oil and lubricants can help reduce wear and tear on engine components. While premium engine oil may be more expensive, it can provide long-term benefits in terms of engine protection and longevity.
- Oil Analysis Programs:Implementing an oil analysis program involves costs associated with collecting oil samples, shipping them to a laboratory, and analyzing the results. However, this proactive approach helps identify potential issues early, allowing for corrective action and potentially extending engine life.
- Upgraded Filters: Investing in higher-quality air and fuel filters can help prevent contaminants from entering the engine, reducing wear and extending the engine’s life. These filters may cost more than standard ones.
- Additives: Some fleets use fuel additives to improve engine performance and reduce wear. The cost of fuel additives is relatively low but can contribute to engine longevity.
- Coolant Maintenance: Proper maintenance of engine coolant, including regular flushing and replacement, can prevent overheating and corrosion, which can extend the life of engine components. These maintenance tasks come with associated costs.
- Regular Inspections: Conducting regular engine inspections and diagnostic tests to identify and address issues early can help prevent major breakdowns and prolong engine life. These inspections may require diagnostic equipment and labor costs.
- Driver Training: Investing in driver training programs to promote fuel-efficient and engine-friendly driving habits can contribute to engine longevity. Training costs can include materials, instructor fees, and driver time.
- Emission System Maintenance: If applicable, maintaining emission control systems like Diesel Particulate Filters (DPF) and Selective Catalytic Reduction (SCR) systems is essential for engine longevity. Costs include cleaning, maintenance, and potential replacements.
- Engine Rebuilds or Overhauls: In some cases, fleets may choose to invest in engine rebuilds or overhauls to extend engine life significantly. While these are major investments, they can be cost-effective compared to purchasing new engines.
- Technology and Telematics: Investing in engine monitoring and telematics systems can help track engine performance and health in real-time, allowing for proactive maintenance. These systems come with hardware and subscription costs.
- Warranty Programs: Some fleets may opt for extended warranties or maintenance contracts that cover engine repairs and replacements, reducing the financial burden of unexpected engine-related expenses.
- Retirement or Replacement Planning: Part of improving engine longevity may involve developing a plan for retiring or replacing older trucks in the fleet. This planning involves financial considerations and budgeting for new acquisitions.
While there are upfront and ongoing costs associated with improving engine longevity in a truck fleet, these investments can lead to long-term savings by reducing breakdowns, minimizing repair expenses, and extending the life of valuable assets. Fleets should carefully assess the potential return on investment (ROI) and prioritize maintenance practices that align with their specific operational needs and objectives.
Resale Value: Well-maintained trucks with a history of regular oil analysis and maintenance tend to have higher resale values. Potential buyers are more likely to pay a premium for used trucks with documented maintenance records.
Regular oil analysis and maintenance for trucks can provide cost justifications in several ways, including contributing to higher resale values. Here’s how these practices can lead to increased resale values and overall financial benefits:
- Extended Engine Life: Regular oil analysis helps identify engine issues early, allowing for timely maintenance and repairs. Addressing problems promptly can prevent major engine damage and extend the overall life of the engine. Trucks with engines in better condition command higher resale values.
- Reduced Repair Costs: By proactively addressing engine issues identified through oil analysis, fleets can avoid costly breakdowns and emergency repairs. This reduces the need for expensive repairs and parts replacements that could negatively impact the truck’s value.
- Improved Fuel Efficiency: Well-maintained engines tend to operate more efficiently, which leads to better fuel economy. A truck with a history of regular maintenance and optimal engine performance can be more attractive to buyers and command a premium price.
- Documented Maintenance Records: Regular maintenance and oil analysis result in well-documented maintenance records. These records demonstrate that the truck has been properly cared for and can instill confidence in potential buyers, allowing them to make informed purchasing decisions.
- Compliance with Manufacturer Recommendations: Many truck manufacturers recommend regular oil analysis and maintenance as part of their warranty programs. Following these recommendations ensures that the truck remains in compliance with manufacturer guidelines, which can be appealing to buyers who want a reliable, warranty-covered vehicle.
- Environmental Compliance: In regions with strict emissions regulations, well-maintained engines are more likely to comply with emissions standards. Compliance with environmental regulations can make the truck more marketable and protect against potential fines or penalties for non-compliance.
- Fleet Reputation: Fleets known for proactive maintenance and regular oil analysis build a reputation for quality and reliability. This positive reputation can lead to higher demand for their used vehicles and result in higher resale values.
- Reduced Depreciation: Trucks that maintain their performance and condition over time tend to depreciate more slowly than poorly maintained vehicles. Slower depreciation can translate into a higher percentage of the original purchase price when reselling the truck.
- Lower Total Cost of Ownership (TCO): Regular maintenance and oil analysis can lead to a lower TCO for the truck, which includes costs such as fuel, maintenance, repairs, and depreciation. A lower TCO can make the truck more attractive to buyers and justify a higher resale value.
- Higher Market Value: A well-maintained truck with a history of regular oil analysis can enter the used truck market with a higher perceived value. Buyers are often willing to pay more for a truck that comes with documented maintenance and a clean bill of health.
While there are costs associated with regular oil analysis and maintenance, the long-term financial benefits, including higher resale values, reduced repair expenses, and increased overall efficiency, typically outweigh these costs. Investing in proactive maintenance and analysis can be a sound financial strategy for fleet operators looking to maximize the value of their assets.
Environmental Compliance: Some regions have strict environmental regulations, and improperly maintained engines can emit excess pollutants. By ensuring engines are in optimal condition, trucking companies can avoid fines and penalties associated with environmental non-compliance. Trucking companies can justify the costs associated with ensuring environmental compliance of engine performance in several ways:
- Avoiding Regulatory Penalties: Environmental regulations, especially emissions standards, are enforced by government agencies. Non-compliance with these regulations can lead to fines and penalties. Investing in engine performance measures, such as emission control systems and regular maintenance, helps ensure that trucks meet emissions standards, reducing the risk of costly regulatory penalties.
- Compliance with Emission Standards: Many regions have strict emissions standards in place to reduce air pollution. Ensuring that trucks comply with these standards can prevent fines and sanctions imposed by environmental agencies. Fines for non-compliance can be substantial and significantly impact a company’s bottom line.
- Preserving Reputation: Environmental non-compliance can harm a trucking company’s reputation. Negative publicity and public perception of environmental irresponsibility can lead to a loss of business and decreased customer trust. Maintaining a clean environmental record through compliance helps protect the company’s image and goodwill.
- Avoiding Litigation Costs: In cases of severe environmental non-compliance, companies may face legal action from environmental advocacy groups or affected communities. Litigation can result in significant legal fees, settlements, and court-ordered fines. Environmental compliance helps mitigate the risk of such costly legal battles.
- Preventing Damage to Brand Value: Environmental violations can tarnish a company’s brand value and may lead to reduced customer loyalty. Protecting the brand’s integrity and value is essential for long-term business success and can justify the costs of environmental compliance.
- Access to Contracts and Markets: Many clients and contracts require transportation companies to meet specific environmental standards. Failing to comply can disqualify a company from lucrative contracts or access to certain markets. By investing in engine performance and environmental compliance, companies can expand their business opportunities and justify the associated costs.
- Avoiding Vehicle Impoundment: In some cases of severe non-compliance, authorities may impound vehicles until the necessary repairs are made to bring them into compliance. This can lead to significant financial losses due to vehicle downtime and associated penalties.
- Insurance Considerations: Some insurance providers may offer reduced premiums to companies that maintain good environmental compliance records. Lower insurance costs can offset the expenses of compliance measures.
- Sustainability Initiatives: Many customers and shippers prioritize sustainability and environmental responsibility in their supply chain decisions. Demonstrating compliance with environmental regulations and adopting sustainable practices can make a trucking company more attractive to environmentally conscious partners and customers.
- Long-Term Cost Savings: While there are upfront costs associated with improving engine performance for environmental compliance, these measures can lead to long-term cost savings through improved fuel efficiency, reduced maintenance expenses, and increased vehicle longevity.
The cost justification for trucking companies to ensure environmental compliance of engine performance is multifaceted. It encompasses avoiding regulatory fines, protecting reputation and brand value, preventing legal and litigation costs, and accessing lucrative contracts and markets. Additionally, it aligns with sustainability goals and can lead to long-term financial benefits.
Improved Overall Efficiency: Regular oil analysis contributes to the overall efficiency of a trucking fleet. Well-maintained trucks perform better, experience fewer breakdowns, and require less unplanned maintenance, all of which lead to cost savings.
Regular oil analysis can contribute to the overall efficiency of a trucking fleet in several ways, leading to various financial benefits. Here are the key financial advantages of incorporating oil analysis into fleet management:
- Optimized Oil Change Intervals: Oil analysis helps determine the condition of the engine oil accurately. By identifying the oil’s remaining useful life, fleet managers can extend oil change intervals without risking engine damage. This reduces the frequency of oil changes, resulting in cost savings related to oil, filters, and labor.
- Preventative Maintenance: Oil analysis can detect early signs of engine wear and potential issues such as coolant leaks, fuel dilution, and contamination. Addressing these problems promptly through preventative maintenance can prevent more extensive and costly engine repairs or replacements down the road.
- Reduced Downtime:By identifying potential problems early, oil analysis can help prevent unexpected breakdowns and downtime. This leads to fewer repair-related expenses and ensures that trucks remain in operation, generating revenue.
- Improved Fuel Efficiency:Regular oil analysis can reveal issues that may negatively impact fuel efficiency, such as worn piston rings or dirty fuel injectors. Addressing these problems can lead to improved MPG (miles per gallon) and fuel cost savings.
- Extended Engine Life: Timely maintenance based on oil analysis results can help extend the life of truck engines and other critical components. This reduces the need for premature equipment replacement, which can be a substantial cost for trucking companies.
- Warranty Compliance: Many truck engine manufacturers require regular oil analysis as part of their warranty agreements. Compliance with these requirements ensures that any eligible warranty claims are honored, saving money on costly engine repairs that would otherwise be the responsibility of the trucking company.
- Lower Repair Costs: Early detection of issues through oil analysis can lead to less extensive and less expensive repairs compared to allowing problems to escalate. This results in cost savings on parts, labor, and downtime.
- Resale Value: Well-maintained trucks with a history of regular oil analysis and maintenance tend to have higher resale values. Potential buyers are more likely to pay a premium for used trucks with documented maintenance records.
- Environmental Compliance:Some regions have strict environmental regulations, and improperly maintained engines can emit excess pollutants. By ensuring engines are in optimal condition, trucking companies can avoid fines and penalties associated with environmental non-compliance.
- Improved Overall Efficiency: Regular oil analysis contributes to the overall efficiency of a trucking fleet. Well-maintained trucks perform better, experience fewer breakdowns, and require less unplanned maintenance, all of which lead to cost savings.
Regular oil analysis can result in cost savings related to maintenance, repairs, downtime, fuel consumption, and extended equipment life. These financial benefits contribute to the overall efficiency and profitability of a trucking fleet, making oil analysis a valuable investment for fleet managers.
While engine oil analysis does come with some upfront costs, the long-term financial benefits, including reduced maintenance expenses, extended equipment life, and improved operational efficiency, can more than justify the investment for semi-tractor trailer trucks. It’s essential to consider these factors when making decisions about implementing oil analysis programs in a fleet management strategy.
Michael D. Holloway is a veteran in the industry with 38 years of experience including product research and development, application engineering, program management, technical sales and marketing. He has been involved in the development and certification preparation instruction for lubrication, maintenance, reliability, quality, and safety. He is considered a subject matter expert in condition-based maintenance, reliability, lubrication, oil analysis, wear debris analysis, failure analysis, tribology, and technical writing. Holloway has a patent, earned 4 university degrees, published 11 books, and holds 16 professional certifications. He can be reached at michaeldholloway63@gmail.com
Michael D. HollowayGlobal Technical Manager | SGS